Data is King, or is it?
Considering the amount of emphasis on maintaining compliance to various regulations and standards, it is sometimes difficult for the managing entity determine what is the governing factor. Data is always seen as the absolute – either it is or it is not; however, there is a problem – data is current or it is not. This is illustrated in the way a product is maintained through PLM as an example. Revision B is only valid until Revision C is approved and released. However, what is to say that someone who does not know Revision C exists will know that Revision B is out-of-date? They cannot. For this reason and many others, ISO 9001 was created.
The Quality Management System (QMS) of an Organization
When a company strives to achieve certain levels of quality and a standard of excellence, there are specific steps that need to be taken. These are normally seen as a top-down approach, or it should be driven from higher management to those who perform the daily tasks of actual assembly, machining, engineering, etc. These steps are individual to each business and are not something that is created and forgotten. The Quality plan is revisited over and over again to determine where quality can be improved to the tolerance limits that are set man senior management. Although there may be some variations, the standard top-down approach is the following:
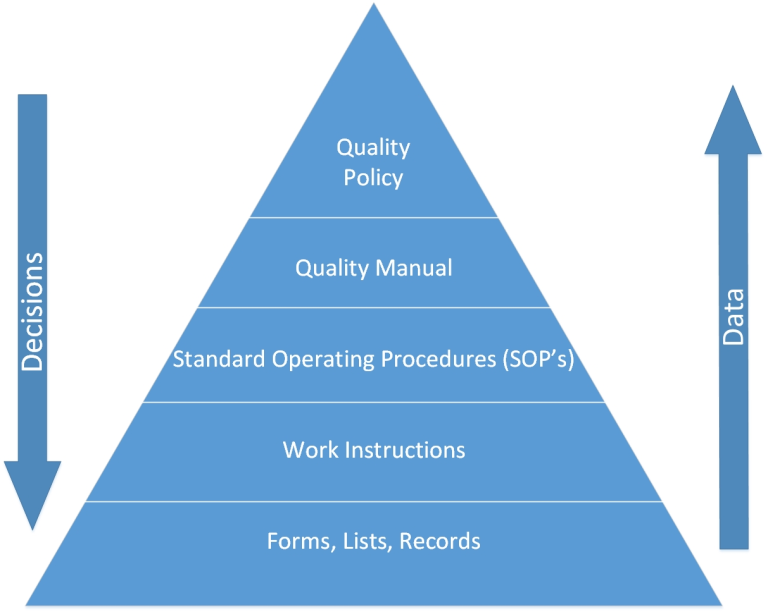
As you can see in the diagram above, the decisions are what drive the formation, but it is the pyramidal base of data that is what feeds the decisions. The QMS policy dictates the manual to be generated, which in turn drives the processes created. Once those have been generated, the processes evolve into procedures which in turn generate data in the form of documents, forms, templates. Vision is what is found at the top, execution at the bottom – each working in harmony to fulfill the QMS Plan.
So why is it that certain companies feel the need to maintain data on drawings that are clearly process-related? If the process trumps data, and data can become obsolete, then it goes to show that the process, which is dynamic, is the preferred strategy. This is echoed in ISO 9001 as you find the emphasis is on the process or procedure, and not on the data requirements. Companies that ignore this concept are similar to the “flat-earthers” of Columbus’ time who fear to venture beyond the visible realm and lose the true vision of what a company should adopt with respect to a QMS. I have had several customers adamantly tell me that in order to maintain ISO 9001 compliance, they had to have the designer, checker, and approver with the accompanying dates on a drawing for each Engineering Change Order (ECO) that was created. This simply is not the case and is akin to returning to a T-square and ruler to make drawings. My suggestion for that customer is to maintain the ECO number on the drawing, which shows the process has been executed and the drawing is approved.
Once businesses begin to understand that the process is of more importance will they begin the transition into the next level of data management. In this day of digital information, the engineer is the last to adopt changes, but once they do, the concept becomes a “no-brainer.”
ISO 9001 in a Nutshell
As this is a simple exploration into ISO 9001, I will only touch on a few requirements that are found it the current version of the ISO standard, namely ISO9001:2008. From there we can extract several requirements that are essential for compliance. The ISO 9001 Application Guide provides insight into what is considered acceptable and what is actually meant when a company claims to be “in compliance”:
“The objective of ISO 9001 is to provide a set of requirements that, if effectively implemented, will provide you with confidence that your supplier can consistently provide goods and services that:
- Meet your needs and expectations
- Comply with applicable regulations
The requirements cover a wide range of topics including your supplier’s top management commitment to quality, its customer focus, adequacy of its resources, employee competence, process management [italics added for emphasis] (for production, service delivery and relevant administrative and support processes), quality planning, product design [italics added for emphasis], review of incoming orders, purchasing, monitoring and measurement of its processes and products, calibration of measuring equipment, processes to resolve customer complaints, corrective/preventive actions and a requirements to drive continual improvement of the QMS.”
Since the QMS and ISO 9001 requirements are complimentary, how does a business know what is the best approach or strategy to take? There are several components that need to be taken into consideration:
- What is management’s commitment to quality?
- What is the level of tolerance that management is willing to accept in order to consider a product or good acceptable or not acceptable?
- Do those QMS criteria have a sliding scale or are there processes and procedures in place that will continually improve quality?
- Are the employees of the company committed to carrying out the QMS and are they proactive enough to identify and report non-conformance anomalies?
- Is there a plan in place to regularly review and identify gaps and issues with the QMS plan?
- Is the customer taken into consideration when creating and executing the QMS?
There are many other questions that can be asked, but with the above in mind, we have a better idea of what ISO 9001 is designed to do and how it can improve quality.
PLM to Lend a Hand!
Since PLM is a controlling software (although sometimes difficult to admit), it is not something that companies want to adopt readily when the assumption is, ‘why do we need it, when we are making money and customer complaints are relatively minor?’ This may be true for weeks, months or even years, however it is usually a major catastrophe that costs the company thousands or even millions of dollars to correct and puts the company’s reputation on the line when quality or the lack of it becomes brutally clear.
To better understand how PLM contributes to compliance, I have attached a document that steps through several of the relevant requirements and how PLM can provide added compliance in doing the following:
- PLM establishes a process by which the engineering process is maintained. This includes New Product Introduction (NPI), Engineering Chane Notice (ECN), Engineering Change Order (ECO), and sometimes a quality document approval process.
- A Non-Conformance Request (NCR) and other quality processes can also be maintained in PLM if another quality software system not specifically created for this cause is available.
- By providing a process that is repeatable and traceable, each step taken during the approval process can be reviewed and evaluated in determining quality improvement areas. Some may become stark and uncomfortable, but if the company understands the need and is willing to take the steps necessary to improve, the changes may be awe-inspiring. It all depends on the company culture and the effort put into the remedies identified.
- Because PLM is a collaborative tool, it brings several departments together and can, if implemented and utilized properly, break down the proverbial silos that plague most companies. The strength in allowing access to data and processes permit management and quality to review and identify where breakdowns in communication are creating bottlenecks in the process. Sometimes it is personnel, sometimes it is management, sometimes the process itself – but if it is not reviewed, frustration, affected revenue and a propagated lack of resolution are the results.
The following document was written with Infor PLM Discrete in mind, but most PLM solutions cover the basics and will provide a better handle on engineering design and processes.
20141105 – ISO9001-2008 – How PLM Contributes to Conformity
Cheers!
Brian